Die Korona-Oberflächenbehandlung wird heute oft bei Druck-, Verarbeitungs- und Laminieranwendungen eingesetzt, spielt jedoch eine noch grundlegendere Rolle im Extrusionsprozess. Giuseppe Rossi ist der Spezialist von Vetaphone für diesem Bereich und erläutert die Notwendigkeit des Prozesses und wie die Technologie auf Änderungen der Marktnachfrage reagiert.
Warum ist die Oberflächenbehandlung im Extrusionsprozess so wichtig?
Tatsächlich zeigt sich die Wichtigkeit der Oberflächenbehandlung im Extrusionsprozess erst später. Um eine gute Haftung von Tinten und Lacken in nachgeschalteten Konvertierungsprozessen sicherzustellen, muss die Molekülstruktur der Filmoberfläche modifiziert werden. Dies muss unmittelbar nach der Abkühlphase der Schmelze erfolgen, bevor das Polymer vollständig nachkristallisiert ist. Durch die Korona-Oberflächenbehandlung zu diesem Zeitpunkt können wir die Molekülketten brechen und der obersten Schicht des Polymers (bis zu 1 Mikron tief) mehr Sauerstoffatome hinzufügen. Dies verändert die Oberflächenspannung und verbessert die Haftung. Je später im Prozess die Oberfläche behandelt wird, desto schwieriger ist es, die Molekülketten zu brechen. Tatsächlich wird dies dann oft unmöglich, daher ist das Timing entscheidend.
Gibt es unterschiedliche Anforderungen für Blasfolien- und Flachfolienextrusion?
Am häufigsten wird die Korona-Behandlung in der Blasfolien-Extrusion verwendet. Aufgrund des hohen Vorkommens von LDPE in diesem Prozess sowie der relativ langsamen Produktionsgeschwindigkeit im Vergleich zur Flachfolienextrusion oder einem der Konvertierungsprozesse benötigt das Korona-System nur wenig Energie, um ein gutes Ergebnis zu erzielen. Die Technologie in diesem Sektor ist gut integriert und ausgereift, und ermöglicht bei guter Steuerung die Herstellung und Behandlung von gleichbleibend hochwertigen Filmen.
Die Flachfolienextrusion ist ein weitaus anspruchsvollerer Prozess, da das PP-Material und die höheren Anlagengeschwindigkeiten ein komplexeres Korona-Systemlayout erfordern. Eine einseitige Vorbehandlungsanlage (im Gegensatz zu doppelseitigen Anlagen bei der Blasfolienextrusion) benötigt normalerweise eine höhere Leistung, eine gekühlte Koronawalze, einen Direktantrieb und eine Andruckwalze – und ist meist als Zugstation ausgelegt.
Es gibt eine dritte Art der Extrusion, die für bi-orientierte Flachfolien wie BOPP, BOPET und BOPA gilt, bei denen die Anlagenbreite und die hohe Leistung erfordern, dass die Korona-Einheit im Extruder enthalten ist.
Sind die Anforderungen auch abhängig vom extrudierten Material?
Ja. Es kommt sehr auf das Material und den nachfolgenden Konvertierungsprozess an. Zunächst einmal hat jedes Polymer seinen eigenen, ursprünglichen Dyn-Wert – dieser beziffert die Oberflächenspannung und die Eigenschaft, ob sich Tinten und Lacke anhaften können. Einige Materialien, wie PVC oder PA, benötigen nur sehr wenig Energie, um die Oberfläche auf den gewünschten Dyn-Wert zu behandeln. PE benötigt etwas mehr Energie, und PP ist bekanntermaßen am schwierigsten zu behandeln. Man muss auch die in den Polymeren enthaltenen Additive berücksichtigen, da diese das Ausmaß der erforderlichen Korona-Behandlung und den Stromverbrauch erheblich beeinflussen können.
Das alles berücksichtigt – welchen Nutzen bietet die Vetaphone-Technologie Firmen in der Extrusionsbranche?
Es ist alles auf gutes Design zurückzuführen, das für Vetaphone-Systeme von Beginn in den 1950er Jahren an von grundlegender Bedeutung war, als das Unternehmen die sogenannte Korona-Behandlung erfand und Pionierarbeit leistete. Zwei Prinzipien zeichnen die Produkte von Vetaphone aus: Einfachheit und hohe Effizienz. Durch das Entwerfen und Herstellen einer benutzerfreundlichen Einheit erleichtert Vetaphone das Reinigen und Einstellen mit seinem Schnellwechsel-Elektrodenkassettensystem. Dies gepaart mit hocheffizienten Generatoren, die den patentierten Resonanzkreis verwenden, ermöglicht es 96% der Eingangsleistung direkt an die Elektroden zu liefern. Das reduziert die Verlustwärme, was ein offensichtlicher Vorteil ist, wenn Sie dünne, sensible extrudierte Folien handhaben. Natürlich gibt es andere Faktoren wie die hochentwickelte Steuerung, die über unsere iCC7-Fernbedienung verfügbar ist – aber im Wesentlichen sind Einfachheit und hohe Effizienz die Hauptvorteile.
Wir sprechen bei der Oberflächenbehandlung immer von Korona – gibt es in der Extrusion auch Anwendungen für Plasma?
Nicht wirklich – aber Sie müssen den Unterschied zwischen den beiden Prozessen kennen, um zu verstehen warum. Plasma ist kein Ersatz für Korona – es ist eine andere Art der Behandlung der Oberfläche bestimmter Substrate, die sowohl eine chemische als auch eine physikalische Behandlung erfordern. Es findet eher Anwendung in speziellen Offline-Konvertierungsverfahren, bei denen die chemische Struktur des Materials sehr komplex ist und einen sehr hohen Dyn-Wert erfordert, den Korona nicht erreichen kann. Plasma erfordert eine kontrollierte Atmosphäre und die Verwendung verschiedener Dotiergase – und zudem ist Plasma erheblich teurer als Korona und wird daher nur in speziellen Situationen verwendet.
Wie hat sich der Extrusionsmarkt in den letzten Jahren verändert?
GR: Der Extrusionsmarkt hat sich verändert, da sich die Märkte, die beliefert werden, geändert haben. Wenn Sie 20 Jahre zurückgehen, waren die meisten extrudierten Folien für den Einsatz im technischen und industriellen Verpackungssektor bis zu fünf Schichten dick. Heutzutage, da der Schwerpunkt mehr auf der Erfüllung der ständig wachsenden Anforderungen der Lebensmittel-, Pharma- und Hygienemärkte liegt, sind Verpackungen mit bis zu 13 Mehrfachschichten weitaus häufiger und das Produkt muss eine Vielzahl von neuen Anforderungen erfüllen. Dazu gehören Frischhaltung, Schutz gegen äußere Einflüsse und Recycling, und dies sind komplexe Probleme für die Hersteller. Nehmen Sie die aktuelle dramatische Situation mit der COVID19-Pandemie, die die entscheidende Rolle hervorhebt, die Verpackungen in unserem täglichen Leben und Wohlbefinden spielen. Situationen wie diese treiben die Nachfrage nach neuen Technologien und zukünftigen Anwendungen voran, die den Wert sogenannter „cleverer“ Verpackungen steigern. Und alles beginnt mit der Extrusion!
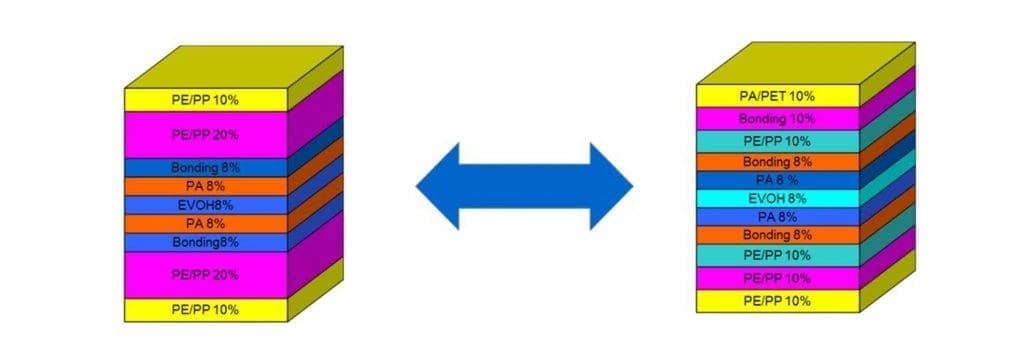
Kunststoffverpackungen scheinen derzeit „Staatfeind Nr. 1“ zu sein – welche Schritte unternimmt der Extrusionsmarkt, um umweltfreundlicher zu werden?
Trotz gegenteiliger öffentlicher Meinung haben Kunststoffverpackungen einen sehr geringen CO2-Fußabdruck in Bezug auf die Herstellung. In Anbetracht des öffentlichen Image und der Notwendigkeit, Verantwortung ernst zu nehmen, würde ich sagen, dass es zwei Möglichkeiten gibt, wie Extrusion dazu beitragen kann, umweltfreundlicher zu werden. Die erste besteht darin, die Verpackung mit neuen Harzen herzustellen, bei denen weniger Kunststoff verwendet werden kann. Dies hilft bei Problemen wie Haltbarkeit und Hygiene, bei denen durch das Extrudieren eines speziellen Materials mehrere laminierte und heterogene Substrate überflüssig werden. Das zweite ist die Art und Weise, wie die Industrie daran arbeitet, die Struktur von Verpackungen zu vereinfachen, indem kompatible Harze verwendet werden, um die Recyclingfähigkeit als Teil der Kreislaufwirtschaft zu verbessern. Das Problem ist nicht die Herstellung von Kunststoff, sondern die Entsorgung nach dem Gebrauch.
Ist das die nächste große Herausforderung der Industrie?
Ja, keine Frage. Wie wir alle wissen, hat sich die EU sehr ehrgeizige Ziele gesetzt, um die Kunststoffproduktion zu reduzieren und das Recyclingniveau zu erhöhen. Es ist jedoch sehr schwierig, den Bedarf an Sauerstoffbarrieren mit der alleinigen Verwendung von Polyolefinen zu erreichen. Eine Lösung besteht darin, bi-orientierte Blasfolien in der sogenannten Triple-Bubble-Technologie zu extrudieren, bei der die Orientierung der Moleküle die Eigenschaften der in Allzweckverpackungen verwendeten Standardharze dramatisch verbessert. Die Sauerstoffbarriere ist nicht so gut wie die von EVOH oder PA, aber gut genug, um einen Großteil der Verpackungen zu ersetzen, in denen sie derzeit verwendet werden. Es gibt keine einfachen Lösungen, aber die Nachfrage treibt Forschung und Entwicklung voran und bringt neue Technologien hervor – das gilt auch für die Extrusion.